22 Millionen Häuser klimagerecht sanieren
ForschungsNotizen der "Innovativen Hochschule Jade-Oldenburg!"
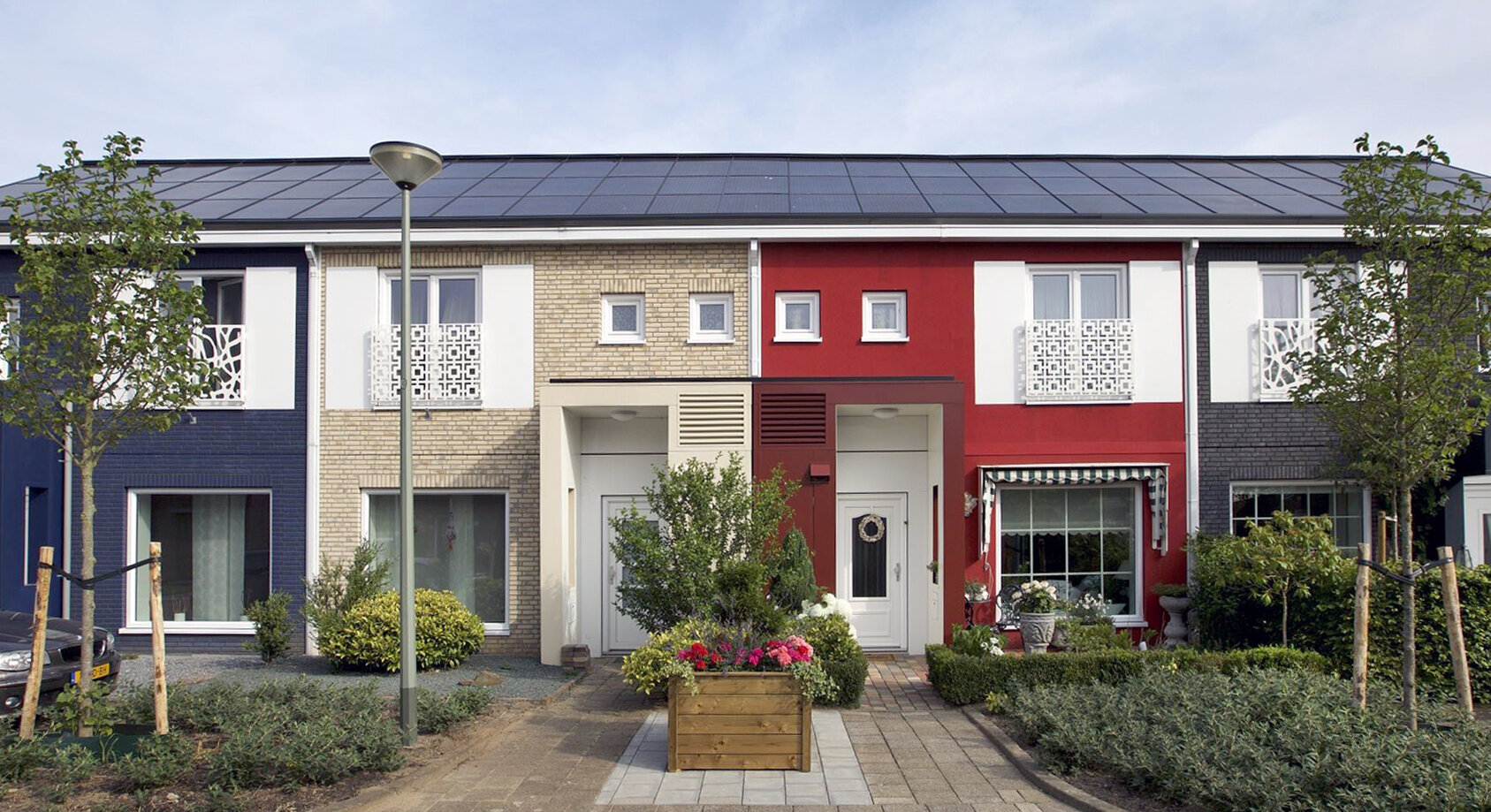
Die Smart Renovation Factory soll helfen, die Klimaziele zu erreichen
Um zur Erreichung der Klimaziele beizutragen, entwickelt das Team des Forschungsprojekts INDU-ZERO eine „Smart Renovation Factory“. Das Konzept zu dieser Fabrik soll als beliebig oft realisierbare Blaupause eine massenweise individualisierte Sanierung von 22 Millionen Häusern im Nordseeraum ermöglichen. Es gibt bereits konkrete Pläne, die Fabrik zu realisieren. Professorin Dr. Kerstin Lange und Bennet Zander von der Jade Hochschule erläutern im Interview, wie die Fabrik aussehen soll.

ForschungsNotizen (FN): Woher kommt das Forschungsziel, eine Blaupause für eine große smarte Renovierungsfabrik zu entwickeln?
Prof. Dr. Kerstin Lange (KL): Mit dem Pariser Klimaschutzabkommen von 2015 haben sich die ratifizierenden Staaten das Ziel gesetzt, die Erderwärmung auf deutlich unter 2 Grad zu begrenzen. In Deutschland verfolgen wir das Ziel, unsere Treibhausgasemissionen bis 2050 um mindestens 80 Prozent unter das Niveau von 1990 zu senken.
An unserem Projekt sind sechs Nordseeländer beteiligt: die Niederlande, Belgien, Großbritannien, Norwegen, Schweden und Deutschland. In diesen Ländern stehen in Summe rund 22 Millionen Häuser, die zwischen 1950 und 1985 errichtet wurden. Aufgrund ihrer veralteten energetischen Standards verursachen sie jährlich CO2-Ausstöße in Höhe von 79 Millionen Tonnen. Gemessen an den Klimazielen ist das zu viel. Um die Ziele zu erreichen, müssen wir auch diese Wohngebäude sanieren und ihre Emissionen verringern.
Die meisten Hausbesitzer und Immobiliengesellschaften scheuen aber die erheblichen Renovierungskosten und die belastenden Renovierungsprozesse. Deshalb gehen die Renovierungen in Bezug auf die Klimaziele zu langsam voran.
Die Fabrik, die wir entwerfen, soll die energetische Sanierung der Häuser nicht nur massenweise mit individualisierbaren Lösungen ermöglichen, sondern die gesamte Sanierung schneller und um rund 50 Prozent günstiger machen. So hoffen wir auf insgesamt schnellere Fortschritte bei den klimagerechten Sanierungen im Nordseeraum.
FN: Was soll die Fabrik am Ende können? Welche Besonderheiten zeichnen sie aus?
KL: Unsere Fabrik soll kostengünstige Sanierungspakete für drei Haustypen anbieten: Reihenhäuser, Doppelhaushälften und Apartment-Häuser. Sowohl die Fertigung als auch die Installation der Sanierungspakete am Haus wird dabei durch unsere Fabrikinfrastruktur betreut. Ein Sanierungspaket enthält eine neue Fassade, neue Dachpaneele inklusive Solarzellen zur Energieerzeugung, Heizungs- und Belüftungspakete.
Bennet Zander (BZ): Die Fabrik hat mehrere Besonderheiten. Erstens soll sie bis zu 15.000 Sanierungspakete pro Jahr herstellen, was eine enorme Menge darstellt, auch in Bezug auf die 15.000 Wohneinheiten, die hiermit entsprechend renoviert werden sollen.
Zweitens soll mithilfe des Blueprints ein Entwurf entstehen, der flächendeckend in den Partnerländern so vervielfältigt werden kann, dass die Sanierungspakete auf kurzen Transportwegen zu den Baustellen im gesamten Nordseeraum gebracht werden können.
Die dritte Besonderheit ist die smarte Produktionsumgebung. In der Wissenschaft bedeutet „smart“ eigentlich nur „intelligent“ und auf Daten basierend. Auf unser Projekt bezogen heißt smart auch autonom und nachhaltig. Es ist unser Ziel, dass sich ausschließlich Roboter als so genannte „cyber-physische Systeme“ in der Fabrik bewegen und jegliche Produktionsprozesse vom Wareneingang über die Produktion bis zum Warenausgang autonom und computergesteuert bearbeitet werden. Hierdurch kann es sogar möglich sein, die umweltfreundlichste Fabrik in Bezug auf nachhaltige Renovierungen weltweit zu sein.
FN: Wie reagiert die Fabrik auf Besonderheiten einzelner Häuser und individuelle Wünsche von Hausbesitzern?
BZ: Die zu renovierenden Häuser werden zunächst über eine heute übliche 3D-Messtechnik ausgemessen und in ein BIM (Building Information Modeling, ein intelligenter Planungsprozess für Gebäude und Infrastruktur, Anm. d. Red.)-Modell übertragen. Die Sanierungspakete sind modulartig und variabel gestaltet, und Architekten beraten den Kunden bei der Planung der Sanierung. Anhand einer vorgegebenen Auswahl schaut man, welche Farben und Materialien sich eignen und geschmacklich passen. Es werden die Spezifikationen hinsichtlich der benötigten Wärme- und Ventilationssysteme geprüft, die sich zwischen Häusern erheblich unterscheiden können. Nach der Beratung kann die automatisierte Herstellung des Sanierungspaketes beginnen.
KL: Hier lautet das Stichwort tatsächlich Mass Customization. Wir sprechen von einer Massenproduktion einer Modulbauweise, auf die sich die Smart Factory festgelegt hat. Die Auswahl der Zulieferer beziehungsweise Hersteller ist dadurch kleiner, aber die wesentlichen Möglichkeiten sind natürlich gegeben, zum Beispiel das für sich sinnvollste Heizungs- oder Solarsystem auszuwählen. Natürlich geht es hier auch darum, die Sanierungen günstiger hinzubekommen. Ein Vorteil ist aber auch, dass dieses Vorgehen die Sanierungsplanung für die Bauherren erheblich vereinfacht. Das ist übrigens auch der Grund, weshalb sich das Projekt auf drei bestimmte Haustypen festgelegt hat. Für Reihenhäuser und Doppelhaushälften ist die automatisierte Sanierung sehr gut planbar, genauso für Apartmenthäuser, da sie sich in Design und Logik sehr ähneln. Sonderfälle, wie zum Beispiel freistehende Einfamilienhäuser oder Bauernhöfe, fallen erst einmal raus, weil keine einheitlichen Gebäudegrößen vorhanden sind und sich deren Paneele somit viel schwerer automatisiert fertigen lassen.
FN: Wie sieht die Fabrik aus?
BZ: Für die Fabrik wurde eine Grundstücksfläche von 20 Hektar angesetzt, weil das eine realisierbare Größenordnung ist. Bis vor einigen Monaten planten wir eine einstöckige Fabrik von 8 Hektar Fläche. Dann haben wir gemerkt, dass die Produktionslinien länger sind als gedacht und wir inklusive der Logistik viel mehr Platz benötigen. Also sind wir auf die Idee gekommen, eine zweistöckige Fabrik zu bauen.
Zweistöckige Fabriken gibt es bisher nur selten. Aber zuletzt hörte ich, dass beispielsweise auch Tesla mit zweistöckigen Fabriken plant. Die haben im ersten Stockwerk ihr Lager und produzieren im Erdgeschoss. Unsere zwei Geschosse verdoppeln auf demselben Grundstück die Kapazität der Fabrik auf 16 Hektar, von daher war das die Lösung für eines unserer größeren Probleme.
FN: Wie sieht die Logistik für diese große Fabrik aus und wie haben Sie sie entwickelt?
KL: Im Projekt unterscheiden wir zwischen der Inbound-, Produktions-, Outbound- und Baustellen-Logistik. Unsere Aufgabe seitens der Jade Hochschule ist die Konzeption der Inbound-, Outbound- und Baustellen-Logistik. Also zum einen die Frage, wie das Material für die Sanierungspakete auf dem Fabrikgelände ankommt, wie es entladen wird und auf welchen Flächen es wie gelagert werden soll. Dann die Fragestellung, wie die Lagerflächen für die fertigen Sanierungspakete aussehen sollen und auf welchem Weg die Pakete das Fabrikgelände Richtung Baustelle wieder verlassen und letztlich vor Ort angebracht werden. In unserer Konzeption arbeiten wir natürlich eng mit den Projektpartnern zusammen, die für die Produktions-Logistik verantwortlich sind.
BZ: Was das Vorgehen betrifft, haben wir zunächst die Logistikflächen berechnet, die wir für das zu lagernde Material benötigen. Das ist komplex. Dafür müssen Sie genau wissen, wie viel Material wie oft am Tag wo benötigt wird. Einen wichtigen Aspekt stellt dabei auch das just-in-time-Prinzip dar. Das Material soll zum benötigten Zeitpunkt sekundengenau zur Produktionsfläche gebracht werden, sodass vor den Produktionslinien keine Pufferbestände gelagert werden müssen oder Staus entstehen. Weiter müssen wir die spezifischen Lagerarten für jedes Material ermitteln. Während man Fensterrahmen ins Regal stellen kann, müssen Flüssigkeiten wie Kleber in Tanks gelagert und über Pumpen zur Produktionsfläche transportiert werden.
Für alle innerbetrieblichen Transportprozesse, die die Materialen zwischen dem Wareneingang, dem Lager, der Produktion und dem Warenausgang bewegen, planen wir außerdem eine selbstorganisierte Beförderung. Statt mit Gabelstaplern arbeiten wir hier mit so genannten AGVs – automated guided vehicles (autonom geführte Fahrzeuge, Anm. d. Red.).
KL: Die Frage nach der Nachhaltigkeit von LKWs führte übrigens dazu, dass wir zurzeit prüfen, ob nicht auch Schiffe für die Logistik in Frage kommen. Diese würden den CO2-Ausstoß der Fabrik gegenüber LKWs nochmal stark verringern.
BZ: Solche Überlegungen sind schon während der Konzeptionsphase extrem wichtig, weil sie sich auf den Standort der Fabrik auswirken. Wenn wir in der Nähe ein Schiff beladen wollen, brauchen wir die Anbindung an Wasserwege.
FN: Wie ist die Logistik nach der Produktion beschaffen, wenn die Teile für die Hausfassaden fertig vom Band laufen?
BZ: Die fertigen Fassadenteile, die vom Band laufen, sind bis zu 22 Meter lang. Hier brauchen wir größere Transportsysteme, die bis zu 5 Tonnen bewegen können. Deshalb denken wir hier zum Beispiel an Deckenkräne. Eine weitere Herausforderung in der Outbound-Logistik ist außerdem die Lagerfläche für die fertigen Module. Wenn es zum Beispiel auf der Baustelle viel regnet, können dort die Fassaden nicht installiert werden. Für solche Fälle brauchen wir bis zu zwei Wochen Pufferfläche im Lager für fertige Fassadenteile. Deshalb gehen wir aktuell von einer gesamten Lagerfläche für die Inbound- und Outbound-Logistik von bis zu 12 Hektar aus. Außerhalb der Fabrik haben wir zurzeit 8 Hektar Lagerfläche für die Logistik geplant, der Rest verteilt sich im Gebäude.
Der letzte Punkt der Outbound-Logistik ist dann die Frage, wie die fertigen Module zur Baustelle kommen. Wie gesagt geht es da aktuell um LKWs, gegebenenfalls zusätzlich um Binnenschiffe, und wir prüfen weitere Transportmöglichkeiten.
FN: Wie gängig sind autonome Fabrik-Konzepte eigentlich?
BZ: In der Wissenschaft sind Konzepte von Smart Factories schon weitestgehend erläutert, definiert und aufgesetzt. In der Praxis ist das noch nicht der Fall. In der gegenwärtigen Industrie ergänzen sich die Roboter und Menschen. Sie arbeiten sozusagen Hand in Hand. Zum Beispiel in der Autofabrik werden die schweren manuellen Prozesse Robotern überlassen, die für Menschen eine gesundheitliche Belastung darstellen, wie zum Beispiel das Zusammenschweißen schwerer Autotüren.
Dass eine Fabrik aber von der Entladung der LKWs über die Produktion bis zur Beladung der LKWs mit dem fertigen Produkt menschenleer ist, das hat noch niemand in Angriff genommen. Außerdem ist die Idee der Smart Factory heute noch zu sehr mit der Pharmaindustrie oder der Automobilindustrie verbunden. Also mit sehr kleinen Produkten wie Medikamenten oder, ich sage mal mittelgroßen, wie Autos. Da wir ganze Hausteile automatisiert fertigen wollen – wo Apartmenthäuser 20 bis 30 Meter breit und 15 Meter hoch sein können – bedeutet unser Projekt besonders für das Bauwesen einen immensen Entwicklungsschritt.
FN: Was waren die größten Herausforderungen in der Konzeption Ihrer Fabrik? Mit welchen ungelösten Problemen haben Sie es noch zu tun?
KL: Die größte Herausforderung ist tatsächlich die geplante Produktionsmenge. Wir wollen jährlich 15.000 Sanierungspakete mit einer Fabrik fertigen können. Das klingt erstmal toll. Aber ich weiß noch, wie alle beim Konsortiumsmeeting erstmal geschluckt haben. Je nach Haustyp brauchen wir eine unterschiedliche Anzahl von Elementen. Über Hochrechungen kamen wir auf eine Produktionsmenge von 540 Elementen am Tag, die wir an 250 Tagen im Jahr fertigen wollen. Bennet sagte dann, wir brauchen unter diesen Bedingungen einen Lagerpuffer von zwei Wochen, was schon ambitioniert ist. Bei dieser Lagerdauer brauchen wir alleine eine Inbound-Lagerfläche von 70.000 Quadratmetern! Solche Dimensionen gibt es derzeit bei bestehenden kleineren Fabriken nicht. Aus der Größe der Fabrik und den jeweiligen Produktionsschritten ergibt sich außerdem am Ende eine Taktzeit von 2 Minuten, die für jeden Produktionsschritt bleibt. Das kann sich kaum jemand vorstellen. Diese Aufgabe lösen wir mit einer Produktionslinie von 200 fast Metern, was eine enorme Größenordnung ist.
BZ: …Dagegen fühlen sich die anderen Komplikationen eher wie das normale Tagesgeschäft an. Zurzeit beschäftigen wir uns zum Beispiel mit der Frage, wie wir die Materialien innerhalb der Fabrik vertikal transportieren. Bis vor einigen Monaten hatten wir das Problem ja noch nicht, weil wir noch von der ebenerdigen Fabrik ausgingen. Jetzt haben wir die zwei Geschosse und müssen nicht nur horizontal, sondern auch vertikal transportieren. Die Materialien haben teilweise unterschiedliche Ansprüche an den Transport, wir haben aber nur ein bis maximal zwei vertikale Transportmöglichkeiten, zum Beispiel ein Förderband und einen Fahrstuhl. Ein horizontaler Transport ist viel einfacher, da jedes Material sein eigenes Transportmittel bekommen kann. Aber ich kann schon mal verraten, dass wir dem Ziel ziemlich nah sind.
FN: Gibt es Ansätze, die Fabrik zu realisieren? Was fehlt noch für die Sanierung der 22 Millionen sanierungsbedürftigen Häuser im Nordseeraum, auf die die Fabrik zugeschnitten ist?
KL: Wir sind sehr froh und auch stolz, dass wir an einem Projekt mitarbeiten, das danach wahrscheinlich umgesetzt wird. Konkret soll in den Niederlanden die Fabrik gebaut werden. Es ist bereits eine Fläche in der Provinz Overijssel ins Auge gefasst, auch mit Binnenwasseranschluss. Die holländischen Partner sind gerade dabei, mit interessierten Investoren zu sprechen. Dort steht das Folgeprojekt in den Startlöchern. Das wünscht man sich natürlich für jedes Forschungsprojekt, ist aber nicht immer möglich.
BZ: Der Blueprint für die Fabrik soll in einem Jahr fertig gestellt sein. Dann kann die erste Fabrik in den Niederlanden gebaut werden. Im Projekt liegen wir sehr gut in der Zeit. Von daher können wir aktuell von einem Baubeginn in den Niederlanden im Jahr 2023 ausgehen. Danach bräuchte es natürlich eine Vielzahl von Fabriken in den verschiedenen Partnerländern, um tatsächlich die genannten 22 Millionen Gebäude im Nordseeraum zu sanieren.
FN: Haben Sie noch offene Wünsche in Bezug auf das Projekt?
KL: Wir wünschen uns, dass das Konzept realisiert wird, am schönsten wäre es natürlich, wenn das sogar in Deutschland klappt.
BZ: Einmal durch die eigens-geplante Fabrik gehen und wissen, dass man der Erde dabei hilft, den Klimawandel zu begrenzen.
KL: Ja, es ist immer ein schönes Gefühl, wenn die eigenen Forschungsaktivitäten später in „der Welt da draußen“ umgesetzt werden. Dann wird die eigene Arbeit ihrem eigentlichen Sinn zugeführt. Das ist mir als Professorin an einer Fachhochschule wichtig: Nicht nur im Forscherzimmer forschen, sondern möglichst viel dafür zu tun, dass die Forschungsergebnisse realisiert werden. Wenn das tatsächlich stattfindet und wir an der Hochschule sehen, wie unsere Forschung ins Leben übertragen wird, macht die Arbeit erst richtig Spaß.
Liebe Frau Lange, lieber Herr Zander, vielen Dank für das Interview!
Über die Innovative Hochschule Jade-Oldenburg!
Die Innovative Hochschule Jade-Oldenburg! wurde als Transferprojekt der Universität Oldenburg, der Jade Hochschule und des Informatikinstituts OFFIS, An-Institut der Universität, im Projektzeitraum 2018 bis 2022 mit rund elf Millionen Euro durch die Bund-Länder-Initiative „Innovative Hochschule“ gefördert.
Das Projekt hat innovative Ideen, Hochschulwissen und neue Technologien in die Zielregion getragen und den Bürgerinnen und Bürgern die Möglichkeit gegeben, Wissenschaft aktiv mitzuerleben. Die Verantwortung für den Inhalt dieser Veröffentlichung liegt bei den Autor_innen.